In the U.S., EU, and many countries, medical device labeling is closely regulated, often with specific labeling requirements for individual device types. To comply with regulations, manufacturers must determine:
- The relevant regulations to determine which codes and other data are required on each device.
- Whether the information must be imprinted directly on the device itself or affixed via a label.
Utilizing laser marking on medical devices is a prominent strategy for manufacturers to adhere to industry regulations. Conversely, for some producers, inkjet printing on medical devices, as well as on labels and packaging, serves as their method of choice.
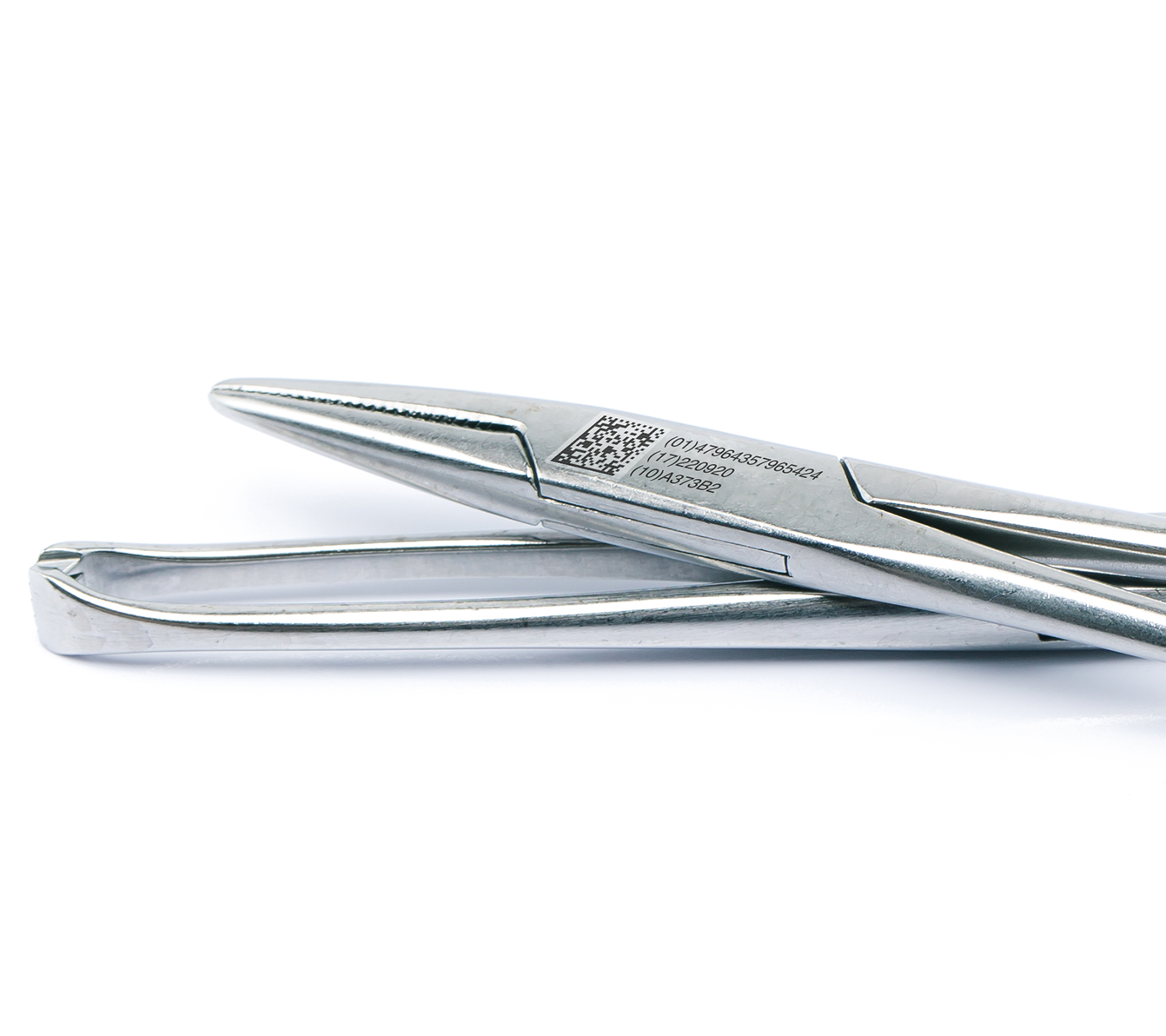
Currently, the U.S., EU, Japan, Australia, Brazil, China, Saudi Arabia, Singapore, and Taiwan are either requiring or in the process of phasing in unique device identification (UDI) requirements for medical device labeling. The implementation of UDI mandates typically occurs in stages based on the medical device’s risk classification. Manufacturers are usually granted an extended period to adhere to these requirements for devices that fall into the highest risk categories.
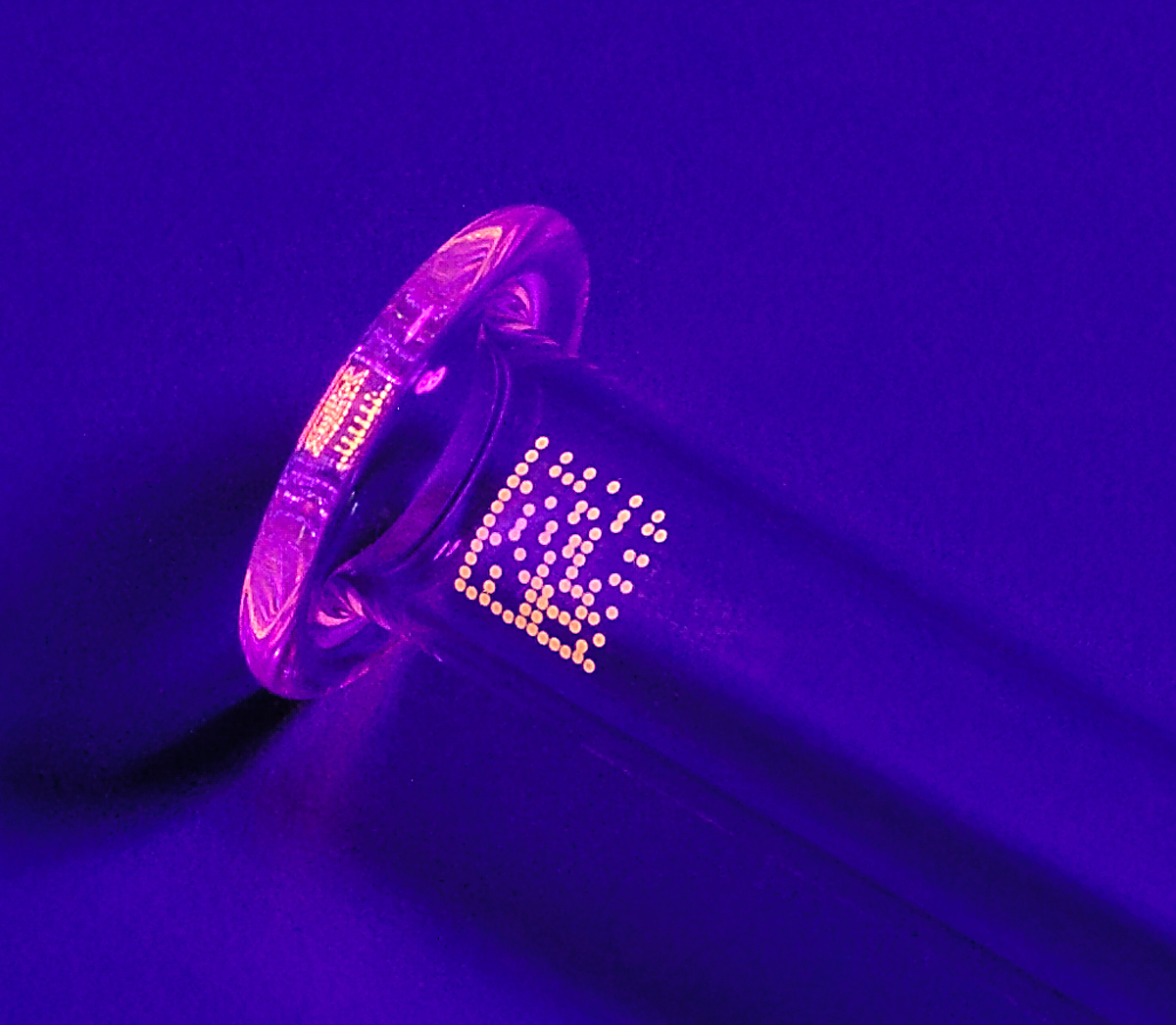
For medical device manufacturers, the selection of a coding solution plays a crucial role in meeting industry regulations. Lasers and printers must be integrated into production lines, manage increasingly complex data without compromising safety or compliance, and produce durable machine-readable and/or human-readable codes.
A UDI code is a unique identifier for medical devices. It consists of two parts:
• The UDI-Device Identifier (static product and manufacturer information).
• The UDI-Production Identifier (dynamic production data such as batch number or expiration date).
The UDI code must be applied to the product both in plain text and in a machine-readable form. For the machine-readable form, the most common codes are DataMatrix, GS1-128, and Code 128.
When choosing marking and coding equipment, consider:
• The equipment’s ability to meet production line speeds
• The ability to maintain optimal code quality
• Integration with selected equipment
• Ease of operation with minimal maintenance needs
With a multitude of medical devices made of various materials, there is no single printing or marking technology that suits them all. Depending on the substrate and other requirements, continuous inkjet (CIJ) printers and laser marking systems are often chosen for printing and marking directly on medical devices.
Yes, Videojet printers and lasers can be installed in a clean room environment with certain considerations to maintain the room’s integrity:
Considerations for continuous inkjet printers in clean rooms
- Ink stream control: The inkjet process involves projecting streams of small drops in a controlled manner. Proper alignment of the ink stream is crucial to prevent any stray drops from becoming airborne particles, which could contaminate the clean room.
- Impact of the room’s environment: Missing drops, that may result from abnormal conditions like excessive air currents or static electricity, might become airborne particles. Such occurrences must be managed to avoid contamination.
- Air supply: Some Videojet printers require a high-pressure air supply that is filtered to ensure the correct operation of the printer. Many clean rooms will already have an adequately filtered air supply. If filtered air is not already present in the clean room, a filter system may be installed outside of the clean room so filter system maintenance does not contaminate the clean room.
Lasers in clean rooms
Fume Extraction: It is mandatory to use a fume extractor wherever a laser is in operation. This is to manage any particulates or fumes generated during the marking process. The fume extractor is necessary even if the room is equipped with an existing air filtration system. Additionally, adequate venting must be installed to replace the extracted air with an equivalent supply of fresh filtered air to maintain the clean room environment.
When choosing between lasers and continuous inkjet printers for UDI marking and other device coding in clean rooms, it is crucial to consider the lifecycle of the product being marked. If the product will require sterilization, permanent laser marking is the ideal solution. Always follow clean room protocols and safety guidelines to maintain the sterility and integrity of the environment.
CIJ printers can mark alphanumeric text, bar codes, and 2D codes on various surfaces, including metal, plastic, and glass. Thanks to their advanced printheads and a wide range of inks, they are suitable for printing on many kinds of syringes, syringe caps, blister packs, and cartons. Requirements for code permanence and resolution must be considered, along with an ink that is well-matched to the substrate to avoid code migration.
Lasers provide high-quality, permanent medical device marking without consumables, aside from fume extractor filters. Depending on the technology—CO2, fiber, or UV—lasers can achieve excellent marks on plastic, metal, and glass. They are ideal for:
• Producing permanent codes on devices like prostheses and surgical instruments
• Withstanding repeated cleaning, sterilization, and use
While lasers and continuous inkjet printers can mark directly on many medical devices, TIJ (thermal inkjet) and TTO (thermal transfer overprinting) solutions are often selected for their high-resolution printing capabilities on medical device packaging. TIJ printers excel at:
• Printing on Tyvek®, blister packs, and cartons
• Being particularly useful in tight spaces on packaging lines
Integrated into packaging machinery, TTO technology is used to print on flexible film packaging, Tyvek, and labels.
Manufacturers must ensure that their printer or laser produces codes with sufficient contrast for machine vision cameras to read codes on small or hard-to-code devices, like syringes. The equipment must also be configurable to the product’s orientation and maintain code quality at line speeds.
State-of-the-art CIJ printers feature:
• Printheads with automatic setup and calibration, adjusting to temperature and viscosity changes, helping to ensure precise drop placement
• Positive air to keep the printhead clean for long runs between cleanings
• An auto-rinse feature to keep the nozzle clean
• A self-contained fluid cartridge design to avoid spills
• A microchip on the cartridge to help prevent errors
High-resolution CIJ printers are capable of producing clear, precise alphanumeric text, DataMatrix codes, and other 2D codes, even at very small sizes. Moreover, CIJ printers offer inks with unique features, like the ability to withstand autoclaving and to fluoresce under UV light, making them perfect for certain syringe coding applications.
Selecting a printer or laser
The choice of marking technology for medical devices should take into consideration the requirements of the application, code, production line, and product lifecycle. Backed by years of expertise in CIJ, laser, TIJ, TTO, and other technologies, Videojet can assess a medical device manufacturer’s unique requirements to help identify the ideal printer or laser for compliance, efficiency, and optimal functionality.
In addition, Videojet supports compliance with GAMP by commenting on the user requirement specification (URS) and providing standardized IQ and OQ documentation. If a standard Videojet printer needs additional features or upgrades to satisfy the URS, Videojet experts will help to develop these features and customize the IQ and OQ accordingly.
Not sure which printing or marking solution is best for your medical devices? Videojet can help with expert recommendations and support, so you can make informed decisions about your operation.
Stay ahead with real-time updates on the latest news: